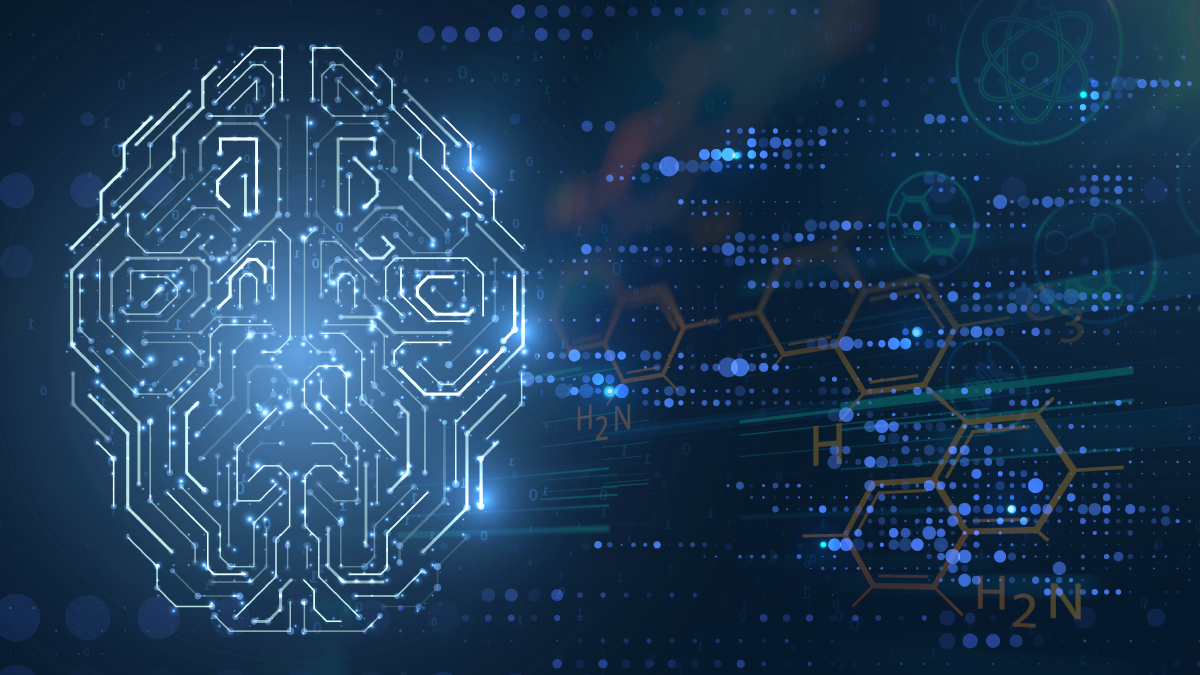
「デジタルトランスフォーメーション」「機械学習」「人工知能」といった言葉は、経営層から研究現場に至るまで、組織内のあらゆる部門で重要な課題となっています。
この投稿は、エンソートのマテリアルズ インフォマティクス(MI)の専門家であるマイケル・ハイバー博士へのインタビューを書き起こしたものです。MIの技術トレンドが材料化学領域の研究開発や製品開発の未来にどのような影響を与えるのかについてQ&A形式で記事にしました。
Q: 化学および材料系企業が直面している主な課題は何ですか?
ハイバー博士:現在の業界で成功するかどうかは、革新的な新材料や化学製品を継続的に開発し、それを事業で活用できる能力に大きく左右されます。これまで高い利益率を誇っていた特殊製品も、次第に一般商品化されつつあり、企業は既存市場で差別化を図り、新興市場でリーダー的地位を確立するために競争を繰り広げています。
一部の企業は競争優位性を得るために、従来のITソリューションやAIプラットフォームに目を向けていますが、これらのツールが研究開発(R&D)ラボでは効果的ではないことを学びつつあります。
科学には独特の特徴があります。そして科学データにも独自の特性があります。製品開発チームは、通常のビジネスデータに比べ、何桁も多い調整可能な変数を扱い、またデータの量は桁違いに少なく、不均一に分布し、時には乱雑なデータを取り扱います。そのため、市販の汎用ツールを単に導入するだけでは解決策にはなりません。
最も効果的なツールは、研究者主導で運用される複雑なR&Dワークフローに柔軟に統合でき、さらにニーズの変化に応じて進化し続けるものです。科学は反復を重ねながら進化し、その可能性に限界はありません。科学用ソフトウェアも同じであるべきです。
Q: 大手特殊化学企業の多くの研究開発(R&D)組織が、機械学習、AI、ロボット自動化に投資を始めていますが、それらを十分に活用できていない理由は何だと思いますか?
ハイバー博士: 企業が意思決定を支援し、製品をより早く市場に投入するための解決策として技術に目を向けるのは当然のことです。しかし、これらのデジタル能力をビジネスに導入・統合するプロセスが不明確であることが多いです。私たちがよく目にするのは、企業がこれらの手法をコーポレートR&Dチームで探求しているものの、そのチームがビジネス部門と非常に乖離しているケースです。
技術や手法は日々進化し続けていますが、現時点でもビジネスに大きなインパクトを与えるだけの成熟度を備えています。マテリアルインフォマティクス(MI)、つまり材料科学とデータサイエンスの融合を最大限に活用するには、技術的成功とビジネス成果を直接結びつける必要があります。そのためには、ビジネスリーダーとR&Dグループ双方からの合意を得ること、研究者のデジタルスキルを強化して従来のR&Dプロセスを加速するための変革を起こすことが重要です。ワークフローや企業文化を変えない限り、プロセスをデジタル化しても既存の形態に制約され続けます。適切な形でMIに投資することで大きな成功を収めている例もあります。
たとえば、エンソートは、電子機器向けの高分子薄膜を開発するラボと密接に協力し、データ駆動型のソリューションを設計しました。このソリューションにより、最適なサンプル製造条件を特定するスピードが100%向上し、材料消費量を50%削減しました。この成果は、彼らのアプリケーションエンジニアリングチームがより迅速に試作を重ね、優れた製品を顧客に提供することを直接的に可能にしています。
また、エンソートは最近、大手石油会社のチームと協力し、二酸化炭素の捕集と再利用のための触媒開発を劇的に加速させるソリューションを開発しました。この結果、目標とする材料特性を予定よりも大幅に早く達成することができました。この取り組みは、新興市場で特殊化学事業を拡大するというビジネス戦略に直接結びついています。
さらに、特殊プラスチックのプロバイダー向けに開発した別のソリューションでは、スケールアップ時のレシピごとに9万ドルのコスト削減を実現し、製品の市場投入期間を数か月短縮しました。これにより、航空宇宙や自動車分野の高級エンジニアリングプラスチック市場で、より多くのビジネスを競うことが可能になりました。
これらの例は、研究開発チームが独自の課題に対応するためのカスタマイズされたデジタルソリューションと必要なスキルを持ち合わせ得たときに、どのようなことが成し遂げられるかを示しています。
Q: 真のデジタルトランスフォーメーションとは何であり、材料系R&Dラボでは、それがどのように実現されるのでしょうか?
ハイバー博士: エンソートでは、「もし科学者たちが有益な発見をするために100%の時間を費やせたら、どんなことが実現可能だろうか?」という問いへの答えを企業が見出すための支援をしています。デジタルトランスフォーメーションの真の価値は、科学的発見を促進し、それがビジネスに対して指数関数的なポジティブな影響を与える点にあります。
データ中心のラボを構築することで、科学者たちはワークフローやプロセスを加速させ、ラボ内でより良く、より迅速な意思決定が可能となり、これまで以上に速く革新的な新製品を市場に投入できるようになります。ルーチン業務の大部分はシステム化・自動化され、研究者は革新的で有益な新しいデータソース(新たな実験やシミュレーション)に注力し、価値駆動型のプロセス改善を継続的に行う体制を整えることができます。
材料系R&Dラボが、科学者が望む製品特性を設定し、その特性を持つサンプルが自動的に生成され、継続的なデジタルイノベーションが組織文化に組み込まれる段階に達したとき、真のトランスフォーメーションが達成されたと言えます。これを実現するためには、研究者と連携する中央集約型のデータサイエンスチームを雇うのではなく、R&Dラボやチームを基盤からデジタル化し、企業全体で多様で分野横断的なチームを形成することが最善です。デジタルイノベーションは分散化されるべきであり、最高のアイデアが生まれ、育まれ、実現される環境を構築する必要があります。
Q: 多くのリーダーが、競争力を維持するためには変革が必要だと認識しています。最初に取り組むべきことは何ですか?
ハイバー博士: 市販のツールを購入しても、自社独自の競争優位性を真に強化することはできません。R&Dにおけるデジタルトランスフォーメーションには、機械学習やAIのさまざまな手法を活用する必要がありますが、最も重要なのは、データサイエンス、ソフトウェアエンジニアリング、材料の専門知識の間でより緊密な連携を築くことです。科学者たちは新たなスキルを習得し、強いデータ文化を採用し、デジタルイノベーションをラボに導入する権限を持つ必要があります。
まずは「低い枝の果実」(Low-hanging fruit:比較的容易に価値を生み出せる課題)を見つけ、解決策を模索することから始めてください。小さな成果であっても、能力構築や社内の賛同を得るきっかけとなり、価値を生み出せば、デジタルプロジェクトへの継続的な投資を正当化できます。このような取り組みは、時間とともに価値と能力の両方を積み上げる形で行うべきです。そうすることで、自社の製品ポートフォリオやR&D専門知識に基づく競争優位性をデジタル領域へ拡張することが可能になります。
ただし、この変革の旅において、「人材」の側面を軽視してはいけません。初期段階では、最もビジネス上の優先度が高い課題よりも、新しいことや革新的なことを試すことに意欲的なチームを選ぶのが得策かもしれません。こうした早期採用者のチームは、適切なスキルと前向きな姿勢を持ち、社内のデジタルチャンピオンや将来のデジタルリーダーとして活躍する素地があります。これらのチームは、将来的により広範な変革を進める上で欠かせない存在となるでしょう。
エンソートがどのように貴社を支援できるかについては、お問い合わせください。
#マテリアルズインフォマティクス #MI #研究開発DX #素材開発 #材料開発
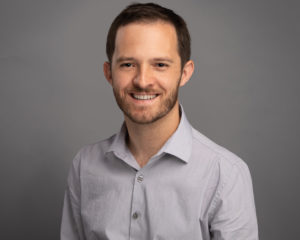
マイケル・ハイバー博士は、エンソートでマテリアルズインフォマティクス領域を専門とするプロフェッショナルサービス及びカスタマーサクセスのダイレクターを務めています。
アクロン大学で高分子科学の博士号、イリノイ大学アーバナ・シャンペーン校で材料科学と工学の学士号を取得しており、特に光電子(こうでんし)用途の高分子(こうぶんし)に関する高い知見を持っています。
エンソートに入社する前は、複数の研究機関でポスドク研究員として、有機エレクトロニクスデバイスの複雑な材料微細構造(ざいりょうびさいこうぞう)と半導体デバイス物理学を結びつける物理モデルの改良に取り組んでいました。
エンソートでは、実験室の自動化、データ駆動型のレコメンデーションシステム、マテリアルインフォマティクス(MI)のトレーニングなど、多岐にわたるクライアントプロジェクトを推進しています。